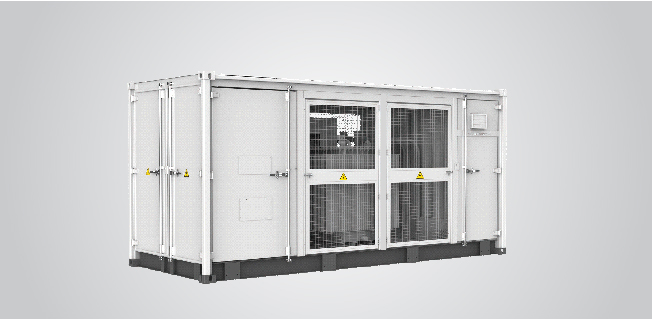
1. Core Challenges in African Manufacturing Plants
1 Unstable Power Supply
Aging grids and insufficient generation capacity plague African nations. For instance, South Africa's 2023 power deficit caused 5%-10% GDP loss, while 97% of Nigerian factories rely on expensive diesel generators (annual fuel costs: $14 billion). Frequent outages disrupt production continuity and damage equipment.
1.2Weak Infrastructure
Remote areas lack transmission networks, and traditional substations require 3–6 months for deployment. Nigeria’s distribution capacity meets only 1/3 of demand.
1.3 High Operational Costs
Self-owned diesel generators have energy costs 3-5 times higher than grid electricity, with added maintenance and fuel logistics expenses.
1.4 Environmental & Regulatory Risks
Extreme climates (e.g., 55°C heat, sandstorms) accelerate equipment wear, while inconsistent regulations delay project approvals.
2. VZIMAN Prefabricated Substation Solutions
2.1 Rapid Deployment & Scalability
- Factory-Prefabricated + On-Site Assembly: Substations are pre-integrated in factories, reducing on-site installation to 2 weeks (70% faster than traditional methods).
- Modular Expansion: Supports "plug-and-play" capacity upgrades to match fluctuating production demands, avoiding redundant infrastructure.
2.2 Climate-Resilient Design
- Extreme Weather Protection: Q345 high-galvanized steel framework with rock wool insulation and EPDM sealing withstands 55°C heat and sandstorms.
- Grid-Independent/Hybrid Operation: Integrates solar storage to reduce grid dependency and optimize energy mix.
2.3 Smart O&M & Cost Efficiency
- Remote Monitoring Platform: Real-time tracking of load, temperature, and equipment health enables predictive maintenance, minimizing downtime.
- Energy Optimization: Dynamic reactive power compensation reduces line losses, cutting overall energy consumption by 15–20%.
2.4 Compliance & Sustainability
- Local Certification: Aligns with African standards (e.g., South Africa SANS, Nigeria SONCAP) to expedite approvals.
- Circular Design: 80% material recyclability and 90% less construction waste align with ESG goals.
3. Expected Outcomes
3.1Production Continuity:
- Annual outage duration reduced from 300 hours to <50 hours.
- Production capacity utilization increases by 30–50%.
3.2 Cost Reduction:
- 40% lower lifecycle costs, including 60% fuel savings and 35% maintenance reduction.
3.3 Faster Project Launch:
- Power infrastructure deployment time shortened from 6 months to 8 weeks.
3.4Enhanced Social Responsibility:
- Reduces carbon emissions from diesel generation, supporting Africa’s energy transition.