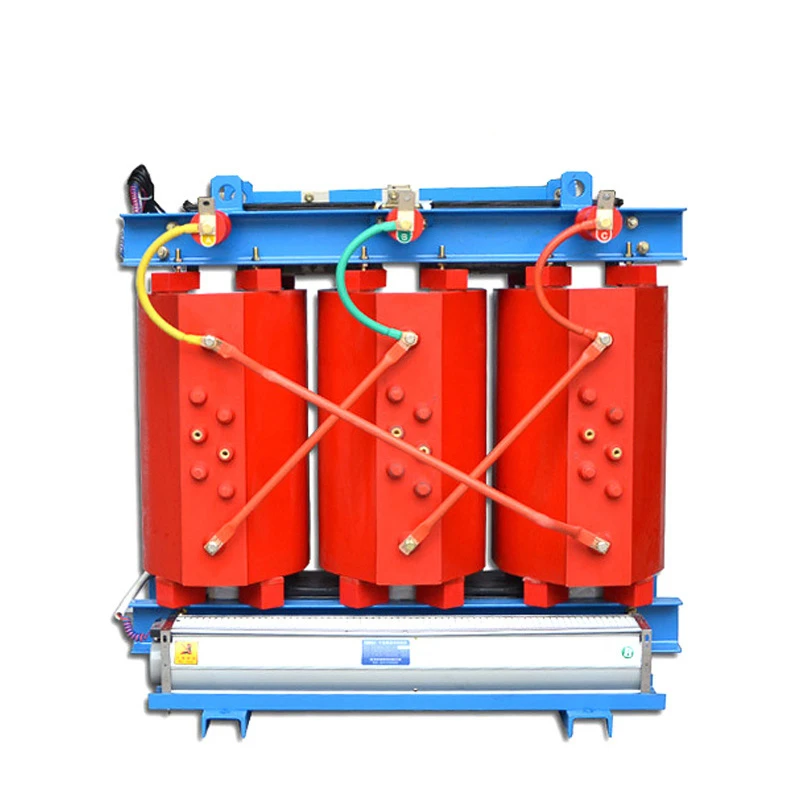
Technical Solution: RW Series Vacuum Pressure Impregnation (VPI) Dry-Type Transformers
I. Core Technological Innovations
- Defect-Free Insulation System
- Utilizes Vacuum Pressure Impregnation (VPI) process to cast high-density epoxy resin, achieving void-free solidified insulation.
- Partial discharge levels stably controlled at <10 pC (IEC 60076-11 standard).
- Insulation thermal class reaches Class H (180°C), with insulation performance degradation rate ≤5% throughout the lifespan.
- Robust Environmental Adaptability Structure
- Integrated casting and sealing technology, achieving IP54 protection (resists persistent dust ingress and water splashing from all directions).
- Flame-retardant grade F1 (per GB/T 2207 standard testing, no sustained combustion under 900°C open flame).
- Wide operating temperature range: -25°C to +40°C (no derating required in areas at ≤1000m altitude).
- Energy Efficiency Optimization Design
- ≥15% reduction** in no-load losses for SCBH15/SCB14 series compared to GB 20052 energy efficiency standard.
- Measured data (1000kVA): No-load loss ≤0.40kW, Load loss ≤7.8kW.
- Dynamic load loss optimization technology, achieving efficiency ≥98.5% within the 35%~100% load range.
- Intelligent Maintenance System
- Embedded PT100 platinum resistors in windings (IEC 60751 Class A accuracy, temperature measurement error ±1°C).
- Supports Modbus RTU/TCP protocols. Enables via IoT gateway:
- Real-time winding hot-spot temperature monitoring.
- Three-phase unbalance analysis.
- Dynamic load-rate energy efficiency assessment.
II. Scenario-Based Application Advantages
Application Scenario
|
Core Problem Solved
|
Technical Implementation Path
|
General Industry
|
Metal dust erosion; Frequent equipment starts/stops
|
IP54 housing seal + VPI pollution-resistant structure
|
Commercial Complexes
|
Stringent fire codes; Compact space
|
F1 flame-retardant grade + Compact design (28% footprint reduction)
|
Data Centers
|
Harmonic pollution (THDi ≤8%); Require 7×24 stable power
|
Anti-harmonic magnetic circuit design + ±2°C temperature control accuracy
|
III. Life Cycle Cost Optimization
Parameter
|
Oil-Immersed Transformer
|
This Solution
|
Benefit Comparison
|
Maintenance Cycle
|
Every 2 years
|
Maintenance-free
|
Saves ¥40k/year in maintenance
|
Failure Rate
|
0.8 per 1000 units/year
|
0.2 per 1000 units/year
|
60% reduction in downtime losses
|
Residual Value (20 yrs)
|
30%
|
55%
|
25% increase in asset value
|
Total Cost of Ownership
|
Benchmark
|
30% lower
|
|
(Validated by TCO Model)
|
|
|
|
IV. Engineering Validation Data
- Accelerated Aging Test: Continuous operation for 5000 hours at 40°C/85% RH; Insulation resistance maintained ≥1000 MΩ.
- Seismic Performance: Passed Class II seismic test per GB/T 13540 standard (horizontal acceleration 0.3g).
- Noise Control: ≤55 dB(A) noise level during operation at 1000kVA load (measured at 1m distance).