1. Accident Overview
1.1 Structure and Connection of 35kV GIS Switchgear Voltage Transformer
The ZX2 gas-insulated double-bus switchgear, manufactured in March 2011 and officially put into operation in July 2012, is configured with two groups of bus voltage transformers (PTs) for each bus section. The two PT groups of the same bus section are designed in one switchgear cabinet with a width of 600 mm. The three-phase PTs are arranged in a triangular formation at the bottom of the cabinet.
The PTs are connected to the disconnectors in the bus chamber of the PT switchgear via short cable plugs. The disconnectors are connected to the three-phase bus through moving contacts in the SF₆ fully-enclosed bus chamber. The fully-enclosed bus structure reduces the failure rate, and the bus is not equipped with dedicated bus protection. Bus faults are cleared through the backup protection of the power incoming switch.
1.2 Operating Mode Before the Burnout
Before the accident, the power grid operated as follows:
- 220kV System: Qiaoshi Line and Huishi Line were running in parallel with the bus tie switch closed.
- Main Transformer Load: No.1 main transformer carried 47 MW, and No.2 carried 14 MW.
- 35kV System: Unit A operated with double buses in split operation. Generator No.2, carrying 30.5 MW, was connected to Bus II of Unit A via Bus 1 of Unit E, the hot oil interconnection line switchgears 361 and 367, and operated in parallel with No.2 main transformer.
1.3 Accident Process
- Fault Precursor
- Starting at 15:11:20.393 on April 19, the protection device of switch 367 in Unit E (Bus Unit for Generators 1 and 2) repeatedly issued PT disconnection alarms, which were intermittently reset.
- Equipment Burnout
- At 15:12:59, smoke and arcing were observed in the PT cabinet of Bus 1 in Unit E. The zero-sequence overcurrent protection of switches 361 and 367 was activated, tripping both switches.
- On-Site Inspection
- The cabinet door was blown open. Phase A PT was severely burned, and the plug of Phase B was fractured. Internal equipment was charred.
- Secondary wires of the adjacent arrester cabinet were damaged. The bus chamber pressure and insulation tests were normal.
2. Cause Analysis
2.1 Equipment Quality and Installation Defects
- Design and Manufacturing Issues
- Poor insulation paint process leading to partial discharge.
- Loose lamination of iron cores causing eddy current heating.
- Irregular coil winding increasing the risk of inter-turn short circuits.
- Installation and Maintenance Defects
- Poor welding of grounding screws increasing contact resistance.
- Deformation of iron cores during transportation/installation.
- Transverse stress from short cable plugs causing epoxy cracking over time.
2.2 Abnormal Operating Conditions
- Secondary Circuit Faults
- Overloading in the secondary circuit due to excessive parallel loops, resulting in increased heat generation according to \(Q = I²rt\).
- Secondary short circuits triggering primary current surges and overheating.
- System Overvoltage
- Ferroresonance caused by switching operations or arcing grounding, generating overvoltages up to 2.5 times the rated value.
- Waveform distortion accelerating insulation aging.
- Three-Phase Imbalance
- High harmonic content (mainly odd harmonics) causing impedance imbalance.
- Neutral point displacement current leading to overheating in the zero-sequence circuit.
2.3 Manufacturer's Disassembly Analysis
- Fault Location
- Epoxy cracking at the flange mounting hole of Phase A PT led to intermittent grounding.
- Mechanical fracture of Phase B plug triggered phase-to-phase short circuit.
- Stress Analysis
- Non-flexible cable connections generated transverse stress concentrated at flange holes.
- Fault progression: Intermittent grounding → Aluminum coating ablation → Fault reset → Final breakdown.
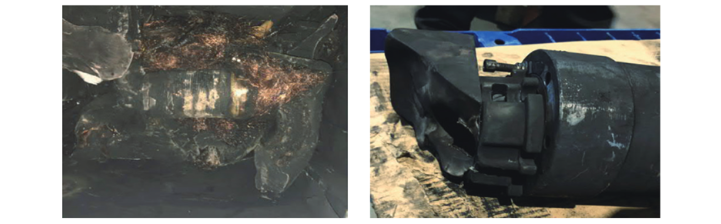
3. Retrofit Plan
3.1 Equipment Monitoring Optimization
- Implement online partial discharge monitoring for GIS switchgears of the same model and establish baseline data.
- Conduct periodic insulation resistance tests with a threshold of 200 MΩ.
3.2 Structural Design Improvement
- Cabinet Expansion: Increase cabinet width from 600 mm to 800 mm to improve heat dissipation.
- Connection Upgrade: Replace short cable plugs with direct connections to reduce stress.
- Modular Design: Adopt pluggable PTs/arresters to minimize maintenance time.
3.3 Protection System Enhancement
- Add dedicated circuit breakers for PT switchgears with overcurrent/overvoltage protection.
- Install dedicated bus protection devices for rapid fault isolation.
- Optimize zero-sequence circuit design to reduce resonance risk.
3.4 Operation and Maintenance Strategy Adjustment
- Establish full lifecycle management records for equipment, documenting installation and maintenance data.
- Perform quarterly SF₆ moisture content tests with a threshold ≤300 ppm.
- Conduct annual PT volt-ampere characteristic tests for comparison with factory data.
4. Lessons Learned and Preventive Measures
4.1 Key Lessons
- Design Flaw: Co-location of PTs increased fault propagation risk.
- Maintenance Gap: Failure to detect cumulative stress damage.
- Protection Deficiency: Reliance on backup protection delayed fault clearance.
4.2 Preventive Measures
- Strengthen equipment manufacturing supervision, focusing on insulation processes and structural integrity.
- Promote condition-based maintenance using vibration monitoring to assess stress levels.
- Revise design specifications to mandate flexible connections between PTs and buses.
- Conduct anti-accident drills to standardize emergency response procedures for PT faults.
4.3 Implementation Results
Post-retrofit data shows:
- Partial discharge reduced from 80 pC to 15 pC.
- Temperature rise under full load decreased by 12°C.
- Fault response time shortened from 600 ms to 40 ms.
5. Conclusion
This accident revealed multiple hidden risks in GIS equipment design, installation, and maintenance. Through structural optimization, protection system upgrade, and management enhancement, a comprehensive risk prevention system has been established. Continuous monitoring of equipment performance will provide replicable retrofit experience for similar substations.