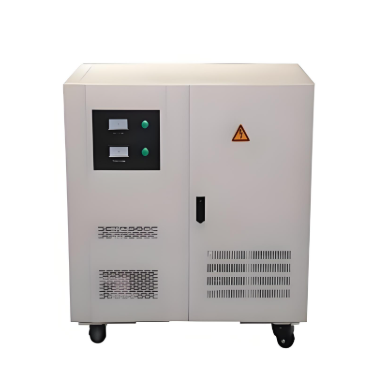
Integrated Solutions for Grid-Connected PV Power Station Transformers: Selection, Design, and Smart O&M
1 Core Functions and Technological Evolution of PV Transformers
In grid-connected photovoltaic (PV) systems, transformers serve as the critical energy conversion hub, with their performance directly impacting the power station’s efficiency and grid stability. Utilizing electromagnetic induction principles, PV transformers boost the low-voltage AC output from inverters (typically 380V–800V) to grid-compatible medium/high-voltage levels (10kV–35kV), enabling efficient long-distance transmission and secure grid integration. This voltage conversion is essential: PV modules generate DC power, which remains at low voltage after inversion. Without step-up conversion, line transmission losses could exceed 20%, severely undermining the project’s economic viability.
1.1 Electrical Isolation and Safety Protection
Modern PV transformers integrate multilayer protection mechanisms for comprehensive safety:
- Electrical Isolation: Blocks residual DC components from inverters to prevent DC bias in grid transformers.
- Short-Circuit Protection: Impedance design limits fault current to 5–8 times rated current, minimizing equipment damage.
- Fire Safety: For oil-immersed transformers, high-ignition-point insulation oils (e.g., natural ester oil, >350°C) reduce fire risk by >70% compared to mineral oil (~160°C), ideal for remote stations with limited firefighting resources.
1.2 Power Quality Optimization
PV transformers directly improve grid compatibility:
- Harmonic Suppression: Built-in dynamic filters and specialized windings (e.g., dual-split design) curb high-frequency harmonics (THD typically <3%).
- Voltage Fluctuation Mitigation: On-Load Tap Changers (OLTC) enable ±10% dynamic voltage adjustment for long-distance transmission or load surges.
Real-world data: A 200MW Saudi plant reduced grid voltage distortion from 4.2% to 1.8% post-optimization, cutting annual downtime by 45%.
1.3 Technology Trends and Innovations
PV transformers are evolving through three key innovations:
- Solid-State Transformers (SST): Replace iron cores with power electronics, achieving >5kHz high-frequency isolation and reactive power compensation. Reduce size by 50% with millisecond response.
- Wide-Band Anti-Interference: Magnetic shielding and RC snubbers suppress electromagnetic noise (1kHz–10MHz), enhancing stability in weak grids.
- Adaptive Dynamic Compensation: Real-time monitoring adjusts winding turns based on current phase changes, compensating voltage sags (response time <20ms).
2 Key Selection Parameters and Optimization Strategies
Transformer selection requires scientific calculation and scenario adaptation. Core parameters determine system efficiency and ROI.
2.1 Capacity Matching and Redundancy Design
Capacity (kVA) = PV Installed Capacity (kW) × Redundancy Factor, where the factor includes:
- Basic Redundancy: 1.1× (for harmonic currents/transient overloads).
- Future Expansion: +0.1–0.15×.
- Environment: +0.05× in high-temperature areas.
Case Study: An 800kW rooftop project selected a 1250kVA dry-type transformer using: 800 × (1.1 + 0.15) = 1000kVA. This handled 1.3× transient overload at noon and supported 200kW expansion in Year 2.
Project Type
|
Capacity Calculation
|
Typical Scenario
|
Recommended Transformer
|
Utility-Scale Plants
|
P × 1.25 + temp. compensation
|
50MW, ambient >40°C
|
Oil-immersed (≥31.5 MVA)
|
Rooftop Commercial
|
P × 1.3 + 0.15× expansion
|
1MW factory, space-constrained
|
Dry-type (1000–2500kVA)
|
Mountain Poverty Allev.
|
P × 1.15
|
200kW, no expansion planned
|
Pad-mounted
|
2.2 Voltage Adaptation and Topology
A three-tier voltage validation ensures stability:
- Primary: Low-voltage (LV) side matches inverter output (±5% tolerance):
- 380V system → 400V inverter
- 660V system → 630–690V inverter
- Secondary: High-voltage (HV) side aligns with grid standards:
- China: 10kV/35kV
- Europe/N. America: 33kV
- Phase: Connection group selection:
- Low-voltage grid: Ynd11 (30° phase compensation)
- High-voltage grid: Dy11 (3rd-harmonic suppression)
Failure Case: A 20MW Vietnam station skipped voltage validation (380V/33kV transformer + 400V inverter), causing insulation aging within 8 months and $230k revenue loss.
2.3 Loss Control and Efficiency Optimization
Transformers account for 15–20% of station losses. Strategies include:
- Core Loss Reduction: Amorphous alloy cores (e.g., SG-B14) lower no-load loss by 60%, saving 42,000 kWh/year for a 1.25 MVA transformer.
- Copper Loss Control: Copper foil windings (+3% conductivity) and liquid cooling reduce load loss by 12%.
- Smart Sleep Mode: Automatic nighttime standby (power <0.5 kW).
ROI Analysis: Though amorphous cores cost 30% more, a 1MW system achieves 37% lower annual loss costs, with a payback period <4 years.
3 Environmental Adaptability and Safety Protection
Diverse deployment environments demand robust solutions across materials, structure, and protection.
3.1 Special Environmental Strategies
- High Altitude (>2000m): Enhanced insulation (power frequency withstand +30%) + sealed radiators. A 3000m Tibet plant reduced winding temperature rise by 15K.
- Coastal High Humidity/Salt: 316L stainless steel + triple coating (zinc epoxy primer, polyurethane mid-layer, fluorocarbon topcoat) → IP65 rating. Hermetic sealing (<5% humidity) prevented corrosion in an 8mg/m³ salt spray environment over 5 years.
- Desert Sand: Labyrinth air filters (99.5% efficiency) + self-cleaning fans extend maintenance to 6 months. Sandstorm auto-switch to internal circulation.
3.2 Structural Protection and Cooling Innovations
- Compact Rooftop Design: Vertical air ducts (+25% cooling area) with low-noise fans (<65dB).
- Integrated Pad-Mounted Units: Combine transformer, ring main unit, metering (<8m² footprint), cutting installation time by 70%.
- Phase-Change Cooling: Paraffin-based materials (70°C melting point) at hotspots enhance sustained overload capacity by 15%.
4 Smart O&M and Lifecycle Management
PV transformer maintenance is shifting from "fail-and-fix" to "predict-and-prevent" using IoT and big data.
4.1 Smart Monitoring and Diagnostics
Three-layer monitoring:
- Core Parameters: Winding temperature (±0.5°C fiber optics), dissolved gas analysis (H₂, CH₄, C₂H₂), vibration spectra (10kHz sampling).
- Edge Computing: Localized analysis triggers protection in <100ms.
- Cloud Platform: Matches fault codes (87% coverage), predicts lifespan (<5% error), auto-generates work orders.
Success Case: A 1MW rooftop system pre-empted interturn short-circuit 72h early, preventing 18kequipmentlossand18k equipment loss and 18kequipmentlossand5.2k/day outage.
4.2 Preventive Maintenance
Data-driven maintenance protocols:
- Oil-Immersed:
- Bi-annual: Oil withstand (>40kV), moisture testing (<20ppm).
- Biannual: IR thermography (alert if ΔT >15K).
- Dry-Type:
- Quarterly: Dust removal (airflow resistance <15Pa).
- Annual: Insulation resistance (>500MΩ).
Lifespan Extension: Dissolved gas analysis (DGA) with deep learning (LSTM) predicts lifespan with 92% accuracy. Proactive tap-changer replacement (after 60k operations) prevents failures.
4.3 Modular Design and Rapid Response
Leading vendors offer modular solutions to boost efficiency:
- Fault location via built-in impedance units (<10min).
- Regional spare parts warehouses (90% delivered in 24h).
- Plug-and-play design (<4h replacement vs. 3 days conventional).
- AR-assisted remote support.
Economy: Modular systems reduce repair costs by 45% and generation loss by 38%, ideal for distributed PV.
5 Integrated Solution Recommendations
5.1 Utility-Scale Plant Solutions
- Core: Oil-immersed (natural ester oil).
- Capacity: 10–100 MVA.
- Features:
- Dual-split windings (isolate inverter interference).
- Forced oil circulation (+40% cooling).
- Integrated OLTC (±15% range).
- Case: 31500kVA transformers at a 500MW desert plant achieved 99.3% annual availability.
5.2 Rooftop Distributed Solutions
- Core: Amorphous-core dry-type.
- Capacity: 500–2500 kVA.
- Features:
- Compact footprint (<2.5 m²/MVA).
- IP65 rated.
- Low noise (<65dB).
- Optimizations:
- Roof load verification (<800kg/m²).
- Ventilation clearance (≥1.5m front/rear).
- Surge arrester residual voltage ≤2.5kV.
Industrial Case: A 5MW coastal factory project saved 30% space and reduced O&M costs to $1.2k/year.
5.3 Special Scenario Applications
- Agrivoltaics:
- Elevated installation (>3m height).
- Anti-mildew coating (for RH >95%).
- Ultrasonic bird repellents + insulation jackets.
- Floating PV:
- Buoyant platforms (≥2× weight capacity).
- Multi-sealed enclosures (welded + epoxy-filled).
- Earth leakage monitoring (1mA sensitivity).
- Arctic Areas:
- Low-temperature heating strips (starts at -40°C).
- Synthetic oil (pour point <-45°C).
- Micro-positive-pressure cabinets (anti-icing).