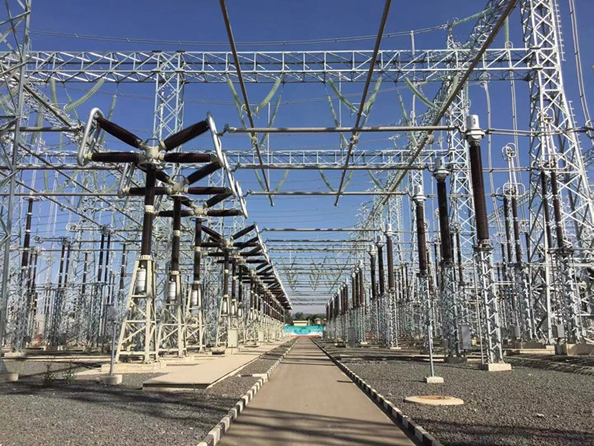
I.Project Background
The Ethiopian highlands feature high altitudes (average over 2,500 meters), extreme cold climates (winter temperatures as low as -30°C), and location within the seismically active East African Rift Zone. These conditions pose significant challenges to power equipment:
- SF6 Liquefaction Risk: At 0.6 MPa operating pressure, SF6 gas liquefies at -25°C. Extreme cold may cause liquefaction, leading to degraded insulation and loss of arc-extinguishing capability.
- Seismic Threats: The region experiences seismic intensities above 8 degrees. Traditional rigid connections are prone to mechanical damage or gas leakage due to geological activity.
- High Reliance on External Maintenance: Local technical expertise is limited, requiring long-term dependence on international contractors for maintenance, resulting in high costs and delayed responses.
To address these challenges, Rockwill must design an SF6 circuit breaker solution tailored to high-altitude, cold, and seismic conditions while ensuring sustainable operation and maintenance.
II. Targeted SF6 Circuit Breaker Design and Installation
- Anti-Liquefaction Design
• Built-in Heating Units: Drawing on proven solutions from China’s frigid regions, nickel-chromium alloy heating strips (800–1,200 W) are integrated at the base of the breaker’s porcelain insulator. Paired with temperature sensors for closed-loop control, this ensures SF6 gas remains above -18°C (exceeding the -25°C liquefaction point at 0.6 MPa).
• Thermal Insulation Optimization: Nanogel aerogel material wraps the porcelain insulator and pipelines, reducing heat loss and improving heating efficiency by 30% in extreme cold.
- Seismic Reinforcement Design
• Flexible Pipeline Connections: Corrugated SF6 gas pipelines allow axial displacement (±15 mm) and radial displacement (±10 mm), preventing seal failure from seismic stress concentration.
• Reinforced Brackets and Isolation Bearings: Brackets use Q345B steel with cross-bracing, while friction pendulum isolation bearings at the base absorb 80% of seismic energy, reducing equipment acceleration response to below 0.3g.
- Localized Maintenance System
• Technical Training Center: A training base in Addis Ababa provides bilingual (English/Amharic) courses focusing on SF6 gas detection, heating system calibration, and post-earthquake equipment evaluation.
• Smart Monitoring System: IoT sensors monitor real-time gas pressure, temperature, and vibration. AI algorithms predict failures and generate maintenance orders, cutting manual inspections by 50%.
III. Expected Outcomes
- Enhanced Anti-Liquefaction Reliability: Heating systems stabilize arc-extinguishing chamber temperatures above -18°C, eliminating SF6 liquefaction risks. Annual circuit breaker failure rates drop below 0.5 incidents per unit.
- Seismic Compliance: Flexible connections and isolation designs enable the equipment to withstand seismic intensities of 8 degrees, with ≥95% functional integrity post-earthquake.
- Optimized Maintenance Costs: Local technician training cycles shorten to 3 months. Maintenance response time improves from 72 hours to 8 hours, reducing lifecycle costs by 40%.
- Environmental Adaptability Verified: The solution has passed -40°C low-temperature tests and simulated seismic platform trials, meeting the composite demands of East Africa’s high-altitude, low-temperature, and high-seismic environments.