Insulation Systems in Oil-Immersed Transformers
The most prevalent insulation for high-voltage windings in modern transformers consists of enamel-coated conductors with kraft paper interlayer insulation.Low-voltage busbars may employ bare conductors with paper insulation between layers.Notably, paper wrapping on busbar conductors is being gradually replaced by synthetic polymer coatings or synthetic fabric wraps.
The adoption of aluminum wires, busbars, and strip conductors with enamel coatings presents specific challenges for distribution transformer manufacturers: aluminum spontaneously forms an insulating oxide layer upon air exposure, which must be removed or mitigated at all electrical connection points.Additionally, electrical-grade aluminum conductors are relatively soft, prone to cold flow and differential expansion issues during mechanical clamping.Splicing methods for aluminum wires include soldering or crimping with specialized tools that penetrate enamel and oxide layers, while sealing out oxygen at contact areas.Aluminum busbars can be welded using TIG (tungsten inert gas) welding, or cold-welded/crimped to copper/aluminum connectors. Bolted connections to soft aluminum are feasible with proper joint cleaning.
Insulation Materials in Dry-Type Transformers
Dry-type transformer windings are typically sealed or coated with resin/varnish to protect against environmental factors causing degradation.Insulation media for primary/secondary windings are categorized as:
- Cast coils: Formed via epoxy resin vacuum casting for superior corona resistance.
- Vacuum-pressure encapsulated: Sealed under vacuum-pressure to enhance insulation integrity.
- Vacuum-pressure impregnated (VPI): Insulation paint infiltrates windings under vacuum-pressure for uniform coverage.
- Coated insulation: Surface coatings provide environmental protection for winding
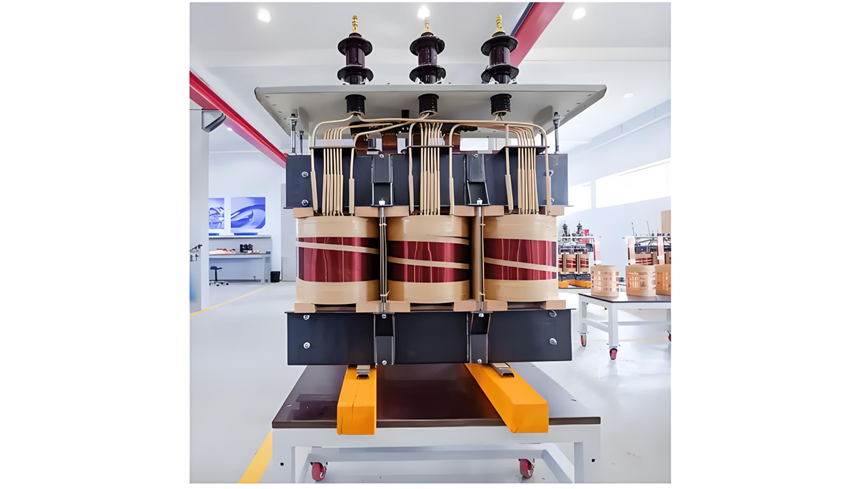
Cast Coil
- The winding is reinforced or placed in a mold and cast with resin under vacuum pressure.
- Encasement in solid insulation minimizes noise levels. Vacuum-pressure resin casting eliminates voids that cause corona.
- The solid insulation system ensures superior mechanical and short-circuit strength, while resisting moisture and contaminants.
Vacuum-Pressure Encapsulated
The winding is embedded in resin under vacuum pressure.Vacuum-pressure encapsulation eliminates corona-causing voids. The winding offers excellent mechanical/short-circuit strength and protection against moisture/contaminants.
Vacuum-Pressure Impregnated
The winding is permeated with varnish under vacuum pressure.Impregnation provides protection against moisture and contaminants.
Coated
The winding is dipped in varnish or resin. Coated windings offer moderate protection against moisture/contaminants for standard environments.