Stator voltage control represents a method employed to regulate the speed of an induction motor. The rotational speed of a three-phase induction motor can be adjusted by varying the supply voltage. As is well established, the torque generated by the motor is proportional to the square of the supply voltage, while the slip at the point of maximum torque remains independent of the supply voltage. Notably, fluctuations in the supply voltage do not affect the synchronous speed of the motor.
The torque-speed characteristics of three-phase induction motors under different supply voltages, along with the characteristics for a fan load, are illustrated below:
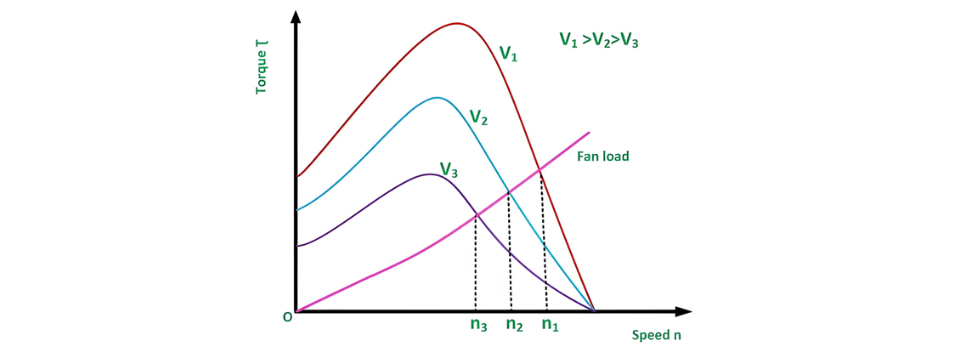
Stator voltage control is a technique used to regulate the speed of an induction motor. The rotational speed of a three-phase induction motor can be adjusted by varying the supply voltage. The torque generated by the motor is proportional to the square of the supply voltage, while the current is directly proportional to the voltage. Thus, the speed is controlled by adjusting the voltage until the motor develops the torque required by the load at the desired speed.
To reduce the speed while maintaining the same current, the voltage is decreased, which in turn reduces the torque output. This stator voltage control method is particularly suitable for applications where the load torque decreases with speed, such as fan loads.
This approach allows speed control only below the normal rated speed, as operating at voltages higher than the rated value is not permissible. It is ideal for drives requiring intermittent operation, as well as fan and pump systems, where the load torque varies with the square of the speed. These drives demand lower torque at lower speeds, a condition that can be met by applying a lower voltage without exceeding the motor's current rating.
For speed control of small-sized motors (primarily single-phase), variable voltage can be achieved through the following methods:
- Connecting an external resistance in the motor's stator circuit.
- Using an auto-transformer.
- Employing a thyristor voltage controller.
- Utilizing a triac controller.
The thyristor voltage controller method is now the preferred choice for voltage variation. For a single-phase supply, two thyristors are connected back-to-back, as illustrated in the figure below:
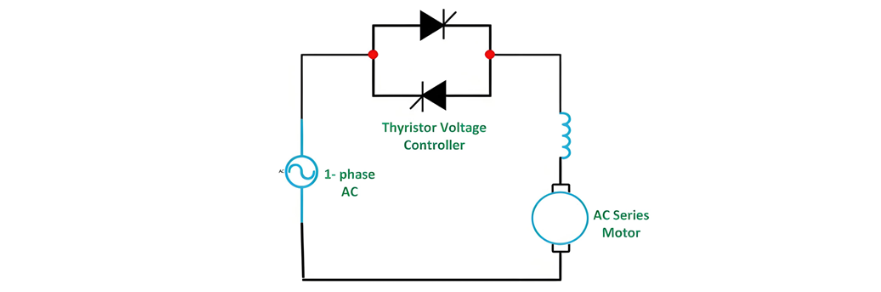
The domestic fan motors, which are single-phase are controlled by a single-phase Triac Voltage Controller as shown in the figure below:
Speed control is achieved by adjusting the firing angle of the Triac. These controllers are commonly referred to as solid-state fan regulators. Compared to conventional variable regulators, solid-state regulators offer greater compactness and efficiency, making them the preferred choice over traditional regulators.
For a three-phase induction motor, three pairs of thyristors are required, with each pair consisting of two thyristors connected back-to-back. The diagram below illustrates the stator voltage control of three-phase induction motors using a thyristor voltage controller:
Each pair of thyristors controls the voltage of the corresponding phase. Speed regulation is achieved by adjusting the conduction period of the thyristors. For lower power ratings, the back-to-back thyristor pairs in each phase can be replaced by a Triac.