In the formula:
- Q is the heat dissipation per unit time;
- ρ is the air density;
- b is the specific heat capacity;
- ΔT is the temperature difference between the inlet and outlet.
Given the potential decline in ventilation efficiency, the measured air flow rate is set to 1.6V. The formula for calculating the effective inlet area A is:

Where v represents the air velocity at both the inlet and outlet. After clarifying the power loss of the transformer control cabinet and determining the expected temperature difference between the inlet and outlet, the required air flow V is calculated using thermodynamic principles. Finally, the specific dimensions of the inlet and outlet are designed based on the air flow V:
- Inlet: width of 0.200 m and height of 0.330 m;
- Outlet: width of 0.250 m and height of 0.264 m.
Analysis of the correlation between inlet pressure loss and opening area reveals that increasing the opening area can effectively reduce gas pressure loss, thereby improving heat dissipation efficiency. On the premise of ensuring the structural strength of the control cabinet, the inlet opening area is set to 0.066 m². To enhance the effective ventilation area, a method combining grilles and louver covers is adopted to increase ventilation passages while preventing the intrusion of dust and rain. In the lower part of the main transformer chamber, an additional air inlet window is installed approximately 40 cm above the ground to further expand the inlet area.
Based on the principle of bottom air intake and top air exhaust, the layout of the inlet and outlet is optimized. The inlet is set at the lower part of the main transformer chamber, and the outlet is located at the upper part, forming natural convection. This allows hot air to rise smoothly and be discharged from the outlet, while cold air enters from the inlet, creating an effective air circulation to improve heat dissipation efficiency.
1.4 Control Cabinet Structure Optimization
To address the unique challenges of salt, humidity, and corrosive substances in offshore wind farms, high-performance anti-corrosion materials and advanced sealing technologies are employed to enhance the overall protection of the control cabinet.
Enhanced Heat Dissipation Design:
- Optimized Ventilation Windows: To resolve inadequate heat dissipation caused by insufficient exhaust windows, additional vents are strategically placed on the top and sides. Calculations determine optimal size and quantity to maximize airflow while maintaining structural integrity:
- 80 top-mounted vents (1.0 m × 0.2 m each);
- 20 side-mounted vents (2.0 m × 0.15 m each).
Cable Entry and Airflow Optimization:
- Rectangular Inlets: Rectangular cable entry ports are machined into the channel steel of the frame base, streamlining cable installation and improving airflow paths.
- Sliding Base Plate: A sliding bottom plate facilitates cable routing to terminals while maintaining effective sealing, ensuring internal components remain protected.
These optimizations result in a structured, well-segregated cable layout that enhances both thermal management and system reliability.
2 Experimental Verification
2.1 Experimental Setup
To validate the feasibility of the heat dissipation design, an experimental platform was constructed to comprehensively simulate the offshore wind farm environment. Two fans were employed to replicate offshore wind speeds and directions. The experimental equipment is listed in Table 1.
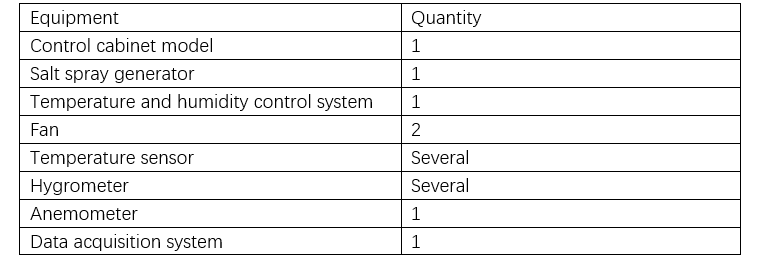
To simulate the offshore wind farm environment, when using fans to mimic wind speed and direction, attention should be paid to wind speed uniformity and direction diversity. Uniform wind speed is crucial for accurate evaluation of the control cabinet's heat dissipation performance, and diverse wind directions can more comprehensively simulate offshore wind direction changes. Thus, during the experiment, fans need to be precisely controlled to ensure wind speed and direction match the actual offshore wind farm characteristics.
2.2 Experimental Results and Analysis
After optimizing the heat dissipation of the offshore wind farm wind turbine box - type transformer control cabinet, the heat dissipation efficiency of different parts of the control cabinet before and after optimization was recorded, as shown in Table 2.
2.3 Results and Discussion
Based on the experimental data in Table 2, the heat dissipation efficiency of the offshore wind turbine pad-mounted transformer control cabinet shows significant improvements after optimization:
3 Conclusion
This study analyzed the impact of the offshore wind farm’s harsh environment on control cabinet heat dissipation. Guided by heat transfer principles, a targeted optimization scheme was proposed and validated experimentally. The optimized design not only improves heat dissipation efficiency and reduces internal temperatures but also enhances corrosion resistance and extends service life. These measures provide robust technical support for the sustainable operation of offshore wind farms.