In recent years, medium-voltage vacuum circuit breakers have witnessed substantial development and achieved remarkable results, especially in the 12 kV voltage class, where vacuum circuit breakers hold an absolute advantage. Currently, the operating mechanisms commonly equipped with 12 kV outdoor vacuum circuit breakers are mostly spring operating mechanisms.
At present, outdoor vacuum circuit breaker products often focus on the design and protection of the main circuit of the circuit breaker while neglecting the service life of the operating mechanism during operation. Ultimately, the entire service life of the circuit breaker is reflected in the opening and closing actions of the contacts, and these actions are realized through the operating mechanism. Therefore, the working performance, reliability, and quality of the operating mechanism play a crucial role in the working performance and reliability of the circuit breaker.
During the long-term operation of the circuit breaker, the failure modes of the mechanism include the refusal of the mechanism to open and close, as well as incomplete opening and closing. The main causes are as follows: damage to the components of the circuit breaker and the mechanism, corrosion of the components of the circuit breaker and the mechanism, the quality of the assembly between the mechanism and the circuit breaker, and faults in secondary electrical components.
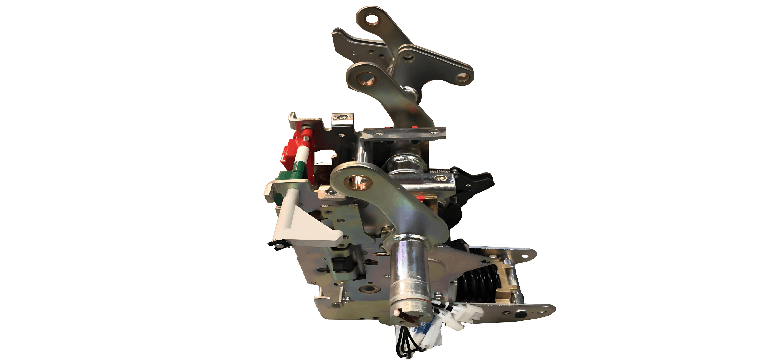
- Reasons for component damage: Firstly, the strength of the components is insufficient during the design process. Secondly, there are misoperations by the operators. Thirdly, the strength of the components is reduced due to corrosion.
- Component corrosion: The corrosion of the components of the circuit breaker and the mechanism leads to jamming of the components, which increases the system resistance. In a corroded state, the opening and closing operation forces of the circuit breaker when it leaves the factory cannot meet the required opening and closing operation forces of the circuit breaker, resulting in incomplete opening and closing. Especially, the reset torsion springs or tension springs widely used in the spring operating mechanism will fail due to corrosion, causing the mechanism to malfunction.
- Assembly quality: The assembly quality of the mechanism and the circuit breaker, mainly including whether the fastening components are reliably fastened and whether the circuit breaker is properly adjusted, will affect the operation of the circuit breaker.
- Secondary electrical component faults: The travel switches, auxiliary switches, and terminal blocks used in the spring operating mechanism. If the quality of any of these components is poor or the contact is unreliable, it will affect the normal operation of the circuit breaker and the transmission of signals, and may even lead to other accidents. In addition to being corroded by moisture themselves, secondary components may also fail to switch normally due to the corrosion of the mechanism components and the jamming of the mechanism movement, resulting in the burnout of the motor or the trip device.
From the above analysis, among the four main causes, the corrosion problem of the mechanism affects three of them. The corrosion problem of the mechanism is the main factor affecting the long service life and high reliability of the circuit breaker.
The corrosion of the mechanism components is the main cause of the failure of the spring operating mechanism. Severe corrosion on the surface of the components seriously affects the appearance of the product, reduces the mechanical strength of the transmission components, and affects the performance of the product. The fundamental causes of component corrosion are the material of the components, structural design, manufacturing process, and especially the surface treatment of the components, which cannot adapt to harsh environmental and climatic conditions.
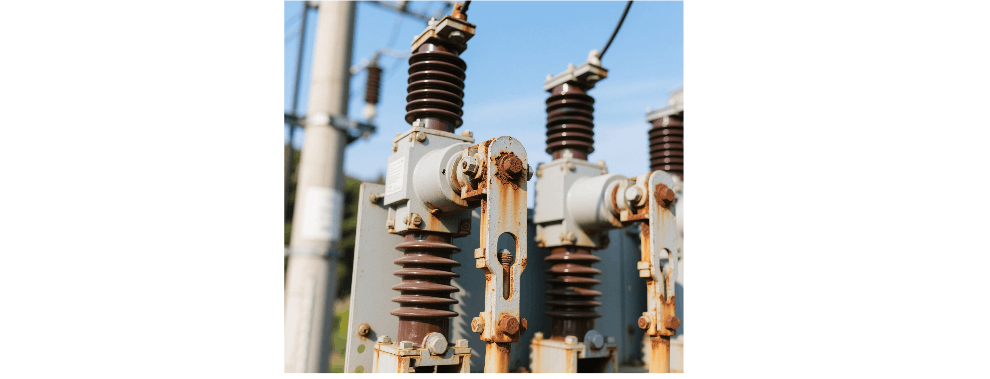
- Influence of metal material quality: The commonly used materials in the product are steel, copper, aluminum, and their alloys. Steel and copper are the main materials in the mechanism. It has been proven that steel components relying solely on a 15 μm zinc plating layer cannot resist the erosion of moisture for a long time. Brass will undergo dezincification corrosion in a humid air environment, and the copper sleeves commonly used in the mechanism will be filled with powder generated by dezincification corrosion in the fit clearance, making the pin shaft unable to rotate.
- Influence of product design structure, component structure, and processing technology: Ball bearings may be corroded due to poor sealing, allowing moisture to penetrate into the bearings. Rust may occur due to water ingress, condensation, and water accumulation. In addition, the gaps, dead corners, grooves, rough surfaces of the components, and the connection points between the components are all areas prone to corrosion.
- Influence of metal surface protection technology: Most of the components of the product are coated with zinc or electrophoretic paint. In the actual mechanism assembly process, for the sake of transmission accuracy, the surface coating is often sacrificed, and the coating on the mating surface and the buckling surface needs to be removed, which contradicts the purpose of surface treatment.
In order to solve the problem of component corrosion, manufacturers usually use a large number of stainless steel components and strengthen the sealing of the circuit breaker and the mechanism. Although using stainless steel as the raw material can improve corrosion resistance, the material price is relatively high, the processing of the components is difficult, and it is not easy to produce in large quantities. Most of the rolling bearings in the standard parts are made of steel, which cannot meet the requirements of corrosion resistance. This method only treats the symptoms rather than the root cause.
Adopting an airtight structure similar to that of ZW20A, without filling SF6 gas, and using a composite insulation form, filling with clean nitrogen to protect the components is a more ideal choice.
In conclusion, the new generation of outdoor vacuum circuit breakers should adopt composite insulation to reduce the volume of the circuit breaker body and meet the demand for miniaturization. The circuit breaker body and the mechanism box should be sealed separately to facilitate the maintenance of the mechanism. Clean nitrogen should be filled to protect the components.