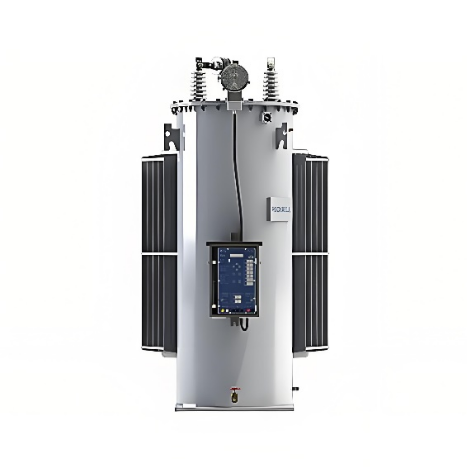
Ⅰ. Analysis of Original Equipment Specifications and System Requirements Assessment
Core Features (ABB RS Series Stepping Voltage Regulator):
- Voltage Regulation Range: 100V-440V AC input, output 0.7-1.0 times rated voltage (e.g., 400V input yields 280-400V output).
- Control Interface: Supports 4-20mA analog signal or RS485 digital communication (Modbus protocol), default parameters: 9600 baud rate, no parity, 8 data bits, 1 stop bit.
- Load Capability: 5A-16A RMS current, suitable for high-power stepping motors.
- Safety Standards: CE certification, IP40 protection level, EN 61800-3 electromagnetic compatibility standard.
- Dynamic Characteristics: Regulation step size: 1-120 steps (STEPS parameter setting), response time ≤20ms.
System Requirements Assessment Key Points:
- Voltage Stability: Base voltage fluctuation ±6% (e.g., 240V±14.4V), ripple voltage <1% (per IEEE 1159-2009 standard).
- Control Precision: Voltage regulation step size must match the original equipment (1-120 steps).
- Communication Protocol: If reliant on Modbus, the replacement device must be compatible or require additional protocol converter configuration.
- Load Characteristics: Confirm current capacity meets requirements; inductive loads require power margin allocation.
- Environmental Adaptability: Operating temperature, humidity, and electromagnetic interference environment must match protection level.
II. Alternative Product Performance Evaluation and Selection Strategy
Possible Alternative Product Types:
- High-Power AC Input Stepping Voltage Regulator: Directly compatible with 100-440V AC input, current ≥16A RMS. Disadvantages: High cost, limited availability.
- Modbus-Compatible Stepping Voltage Regulator: E.g., Leadshine DM2C driver. Requires: External AC/DC conversion module and control board (e.g., JMDM-COMTSM).
- Three-Phase Variable Frequency Drive Single-Phase Operation Solution: E.g., Rokin LV8729, supports wide voltage adjustment (0-300V) and high power (1kVA-100kVA). Requires: Professional configuration.
- Protocol Converter Solution: Use WJ321/WJ181 converters to bridge Modbus and analog signals (0-10V/4-20mA). Advantage: High flexibility. Disadvantage: Increased system complexity.
Selection Strategy:
- Prioritize products directly compatible with original equipment parameters to minimize system modifications.
- Ensure compatibility with Modbus protocol and register mapping to avoid additional configuration.
- Alternative product current capacity must be ≥16A RMS to meet load requirements.
- Must comply with CE, IP40, and EN 61800-3 safety standards.
- Support software upgrades to facilitate system expansion (e.g., via high-precision D/A converters or digital control technology).
III. Interface Adaptation and Control Logic Adjustment Design
Communication Interface Adaptation Solutions:
- Direct Modbus Connection: Verify compatibility of alternative product register addresses with original equipment (e.g., voltage setpoint register).
- Protocol Conversion: Convert Modbus signals to 0-10V/4-20mA analog signals using WJ321/WJ181, or support Modbus TCP communication.
Control Logic Adjustment:
- Step-to-Continuous Conversion: In the PLC, convert step commands (step count N) to voltage values (e.g., V = V_min + N × step value).
- Safety Logic Inheritance: Configure overvoltage/undervoltage protection thresholds to match original equipment, or add external protection circuits.
- Dynamic Response Compensation: If the alternative product response time differs significantly from original (e.g., 20ms → 50ms), add delay compensation in the PLC program.
Physical Interface Adjustment:
- Adapt terminal block layout and design wiring plates to ensure electrical connection reliability.
- Evaluate thermal management system; if alternative product has insufficient cooling, add external heat dissipation devices or adjust mounting position.
- Confirm product dimensions match cabinet space to avoid poor heat dissipation.
IV. Installation, Commissioning Process, and Safety Verification Steps
Commissioning Precautions:
- Progressive Commissioning: Ramp up from low voltage and light load to rated values to prevent equipment damage.
- Data Recording: Compare key parameters (voltage, current, temperature) between original and new equipment.
- Functional Testing: Verify functionalities: overvoltage protection, short-circuit protection, step regulation, and dynamic response.
- Stability Testing: Conduct continuous operation ≥24 hours to observe performance fluctuations.
V. Long-Term Maintenance and Spare Parts Supply Recommendations
Maintenance Plan:
- Regular Inspection: Clean cooling system quarterly; inspect electrical connections semi-annually; assess power module aging annually.
- Performance Monitoring: Record operating parameters monthly; detect output waveform THD (Total Harmonic Distortion) quarterly.
- Software Updates: Upgrade control software regularly to fix vulnerabilities and enhance performance.
Fault Diagnosis Process:
- Initial check: Input voltage, communication lines.
- Detailed diagnosis: Voltage regulation, communication protocols, thermal management system for abnormalities.
Spare Parts Supply Strategy:
- Critical Spare Parts: Power modules (IGBT/MOSFET), cooling fans, communication interface modules, control chips (DSP/FPGA).
- Spare Parts Management: Maintain inventory; collaborate with manufacturers to ensure supply; periodically inspect spare parts status.
- Personnel Training: Familiarize personnel with new equipment technical features; ensure proficiency with manufacturer-provided maintenance resources.
VI. Common Issues and Solutions
Problem
|
Cause
|
Solution
|
Voltage Step Size Mismatch
|
Step size of alternative product differs from original equipment.
|
Implement PLC software compensation for step value conversion; if alternative has finer steps, retain original precision; contact vendor for software upgrade.
|
Communication Protocol Incompatibility
|
Protocol of alternative product does not match original system.
|
Deploy protocol converter; modify PLC communication logic; choose a product with compatible protocols or request vendor adaptation.
|
Insufficient Current Capacity
|
Current rating of alternative product is lower than original equipment.
|
Replace with higher-current product; reduce load or enhance cooling; parallel multiple devices to increase capacity.
|
EMC Compatibility Issues
|
Alternative product exceeds electromagnetic emission limits.
|
Select a product compliant with EN 61800-3 standard; add shielding/filtering; optimize wiring to reduce interference.
|
Improper Temperature Management
|
Insufficient heat dissipation design or constrained installation space.
|
Add external cooling devices; adjust mounting position to ensure ventilation; implement temperature monitoring and protection logic in PLC.
|
Missing Safety Functions
|
Alternative product lacks critical safety features (e.g., OVP, short-circuit).
|
Select a product with comprehensive safety functions; add external protection circuits; supplement safety logic in PLC.
|
VII. Conclusion and Implementation Recommendations
- Prioritize Directly Compatible Products: Minimize system modification risks by selecting solutions like high-power AC input stepping voltage regulators.
- Refine Interface and Logic Adaptation: Ensure compatibility of critical parameters: communication protocol, step size, response time.
- Strict Commissioning and Verification: Test progressively from no-load to full-load, record data to establish performance baseline.
- Effective Long-Term Maintenance Strategy: Ensure system stability through regular inspections, spare parts management, and personnel training.
- Future Expansion Consideration: Choose products supporting software upgrades to facilitate future system iterations.