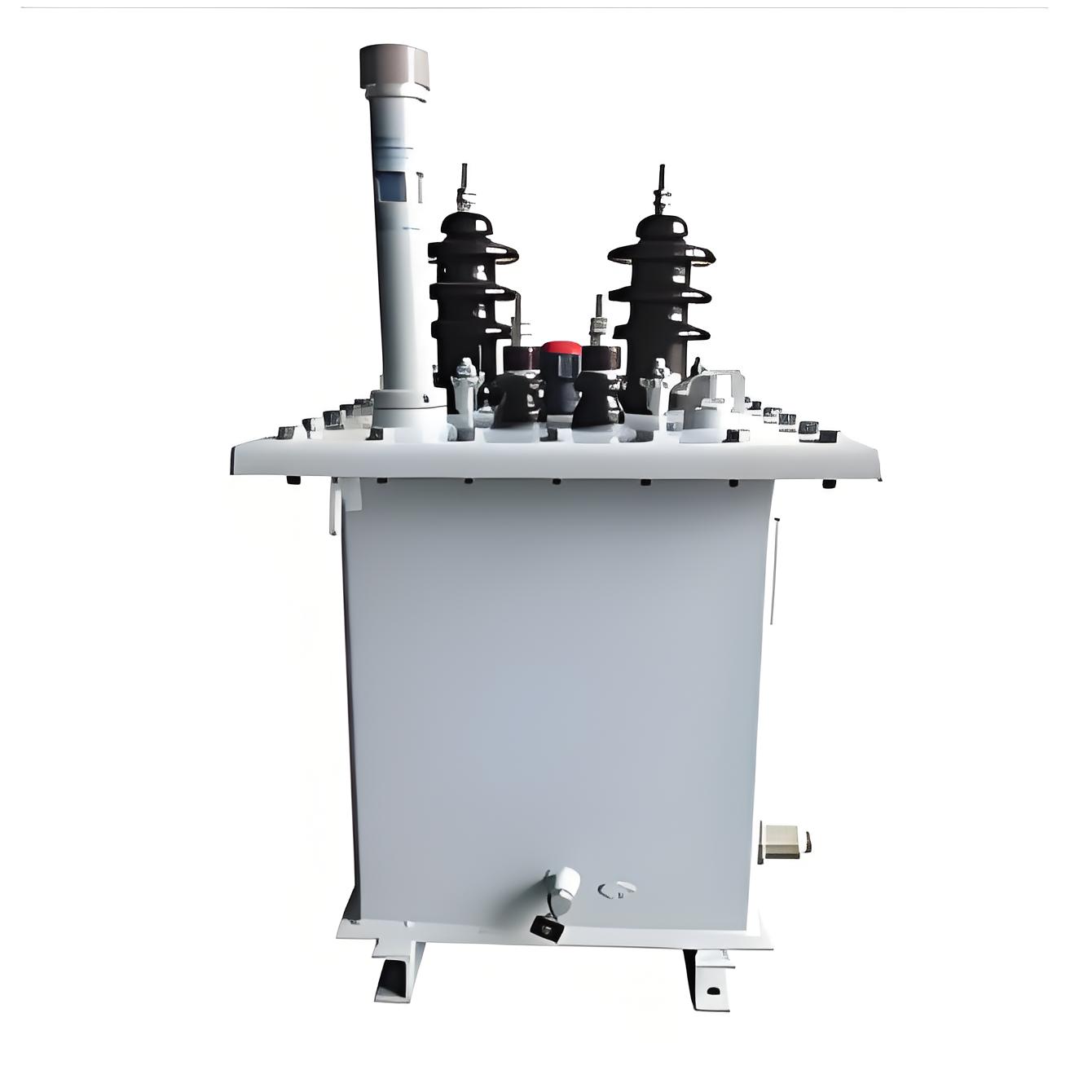
Ⅰ. Characteristics of the U.S. Power System & Technical Requirements for Single-Phase Transformers
The U.S. power system utilizes a 480V/277V three-phase four-wire system as the primary power supply standard for commercial facilities, while residential applications adopt a 120V/240V single-phase three-wire system.
Technical Parameters:
- Input Voltage: Must cover a fluctuation range of ±10% (e.g., 277V ±27.7V).
- Output Voltage Accuracy: Controlled within ±3%.
- Insulation System: Must meet Class H (180°C temperature resistance) standards and pass UL1446 Insulation System Certification.
- Overload Capacity: Sustain 120% rated load for 1 hour.
- Energy Efficiency: Per the DOE 2024 Final Rule (G/TBT/N/USA/682/Rev.1/Add.2), efficiency standards for single-phase dry-type distribution transformers range from 98.31% (15kVA) to 99.42% (1000kVA), achieving 35% energy savings compared to traditional products.
Material Selection:
- Core Material: Iron-based amorphous alloy is preferred to reduce no-load losses. Experimental data show that under identical conditions, amorphous alloy cores reduce core losses by 70–80% compared to silicon steel cores. For a 10kVA transformer, this saves ~1,000 kWh annually.
- Winding Material: High-purity oxygen-free copper wire (conductivity ≥100% IACS), reducing resistive losses by 15% versus standard copper.
- Insulation Material: For medical devices, polyimide film (Class C) and silicone organic paint ensure leakage currents below 50μA (CF-type) or 0.5mA (BF-type).
II. UL Certification & U.S. Market-Specific Requirements
UL Certification is a critical barrier to U.S. market entry:
- UL 5085 Standard: Covers transformers for industrial control equipment, including electrical safety, overload protection, short-circuit protection, and temperature rise limits.
- DOE 2024 Energy Conservation Standards: Require higher efficiency, projected to save 1.71 quadrillion BTU over 30 years.
U.S. Market Demands:
- Safety:
- UL 5085 mandates robust insulation and multi-protection mechanisms (over/under-voltage, overcurrent, overtemperature).
- Medical devices must comply with FDA Class II standards (leakage current: CF-type ≤50μA, BF-type ≤0.5mA).
- Efficiency:
- NEMA TP2 standards emphasize real-world operating efficiency.
- DOE forecasts 1.1% CAGR load growth by 2033, with winter/summer peak loads rising by 91GW/79GW, respectively.
- Environmental Adaptability:
- Commercial buildings (e.g., hotels, data centers): Noise ≤45dB.
- Industrial scenarios: IP54 protection and strict temperature control (ΔT ≤55K @ full load).
- Installation & Maintenance:
- Modular designs with pluggable terminals reduce on-site maintenance time by 70%.
- Installation must avoid flammable/explosive materials and water sources, ensuring adequate ventilation.
III. High-Efficiency Single-Phase Distribution Transformer Design
Design Element
|
U.S. Standard
|
Recommended Solution
|
Performance Advantage
|
Core Material
|
Low no-load loss
|
Iron-based amorphous alloy
|
70–80% lower no-load loss vs. silicon steel
|
Winding Design
|
Mechanical strength
|
Layered multi-strand winding
|
Enhanced strength & heat dissipation
|
Insulation System
|
Class H (180°C)
|
Polyimide film + silicone paint
|
Leakage current <0.5mA; medical compliant
|
Smart Control
|
Remote monitoring
|
Modbus RTU/TCP or NB-IoT
|
Real-time monitoring, fault alerts
|
IV. Scenario-Based Customized Solutions
- Commercial Kitchen Equipment:
- Power demand: 10–50kVA; starting current up to 5–7× rated current.
- Solution: Amorphous alloy core + layered multi-strand winding.
- Compliance: IP54 protection, ambient temperature -25°C to +40°C.
- Example: Dishwasher (10–46kW) uses 480V-to-380V transformer with 80% design margin for high-load stability.
- Medical Devices:
- Safety: Dual insulation + GFI module; leakage current ≤50μA (post-humidity test ≤100μμA).
- Example: MRI transformer with ultra-low ripple (<0.1%) to prevent image distortion; complies with FDA Class II and IP65.
- Industrial Production Lines:
- Reliability: Short-circuit withstand 50kA, noise ≤55dB(A), IP65 protection.
- Solution: Reinforced winding + optimized core support + smart cooling fans (energy saving: 10–15%).
- Residential Applications:
- Power: 500W–2kVA; noise ≤45dB, efficiency ≥98% (Energy Star compliant).
- Example: 120V/240V-to-220V transformer with compact design for wall mounting; meets NEC fire-spacing standards (IP20 for dry indoor environments).
V. Why Choose ROCKWILL
- Cost & Delivery:
- U.S. transformer lead times extend to 120 weeks, with prices up 40–60%.
- ROCKWILL’s factory-direct model enables 7-day delivery of UL-certified transformers.
- Certification:
- Holds both UL 5085 (whole-machine) and UL 1446 (insulation system) certifications, ensuring global recognition.
- Flexibility:
- Modular designs support three-phase 480V-to-380V or single-phase 220V conversion for diverse needs.